Joshua Telson BSE, Dan Ding PhD, Mark McCartney, Rory Cooper PhD
Human Engineering Research Laboratories, Department of Veterans Affairs, Pittsburgh, PA
Department of Rehabilitation Science and Technology, University of Pittsburgh, Pittsburgh, PA
ABSTRACT
The KitchenBot is an overhead track mounted manipulator being designed to aid individuals with upper extremity impairments to complete common kitchen tasks such as meal preparation and cleanup. Focus groups with a total of 26 wheelchair users were conducted to determine common kitchen difficulties and solicit feedback on the preliminary design. Furthermore, Finite Element Analysis (FEA), a method for solving structural analysis problems, was conducted to ensure the design would meet safety requirements. Results from the study showed the proposed track design would withstand mass loading necessary to aid individuals with their most difficult kitchen tasks, i.e., putting away groceries, using the oven, and using the stovetop. Further development and user evaluation of the KitchenBot will ultimately bring to light a unique solution that integrates robotic manipulators to assist with reaching and handling functions in a kitchen.
BACKGROUND
In a survey of 89 wheelchair users and 52 health care professionals, the ability to adequately reach for objects was rated as the most important concern (Holliday, Mihailidis, Rolfson, & Fernie, 2005). Such functional limitations, which are required for interacting within a kitchen environment, can be caused by the natural progression of aging, a medical condition, or trauma. About 1 in 10 adults aged 55 years and over have difficulty reaching (11%) or grasping (9.4%) with rates tripling between the ages of 55-64 years and 85 years and over (Schoenborn & Heyman, 2009). Furthermore, about 1.1 million Americans have experienced serious upper extremity impairments, including those with quadriplegia, hemiplegia, cerebral palsy, and hemiparesis. Approximately half of those individuals with hemiplegia have a non-functional arm and hand even four years after a stroke (Broeks, Lankhorst, Rumping, & Prevo, 1999).
Those individuals with upper limb impairments generally require assistance from caregivers to complete common daily tasks. However, attendants and caregivers suffer from a shortage of resources while their demand continues to increase, causing individuals to leave their homes for costly institutional settings simply for the benefit of receiving basic care (Feinberg, Wolkwitz, & Goldstein, 2006). Consequently, assistive robotic manipulators have emerged as a potential solution.
Traditionally, robotic manipulators have been placed on a mobile base, mounted on power wheelchairs, or installed in fixed locations. For example, several research initiatives seek to provide a mobile assistive robotic solution. HERB, a robotic butler, focuses on providing a mobile base manipulator with intelligent control software capable of detecting objects, planning grasp methods, and navigating environments (Srinivasa et al., 2009). Also, the MANUS arm is a multi-degree of freedom manipulator designed for power wheelchair users to assist with task completion. Furthermore, the Personal Mobility and Manipulation Appliance (PerMMA) is an advanced example of a power wheelchair equipped with dual MANUS arms for local or remote controlled task execution (Xu et al., 2010). All of these former solutions have shown to be useful for completing simple retrieval or multi-step tasks but present complex control algorithm challenges before they can become commercially available. The downfall to mobile robotic systems is the complexity needed to perform navigation, mapping, and sophisticated trajectory planning in an environment that is unstructured and constantly changing (Srinivasa et al., 2009). Furthermore, not everyone uses powered mobility for independence, nullifying wheelchair-mounted arms as the best universal solution. Nevertheless, other possibilities exist, such as the Desktop Vocational Assistant Robot (DeVAR), which is an example of a manipulator mounted in a fixed location on an overhead track for assistance in the workplace (Taylor, Cupo, & Sheredos, 1993). This design was shown to be beneficial for task completion and will be later explained.
A survey of 42 individuals with limited or no upper extremity ability revealed the kitchen was considered the best site for accommodating an assistive robotic device (Stanger, Anglin, Harwin, & Romilly, 1994). Consequently, the KitchenBot is aimed at reducing caregiver needs in the kitchen so individuals may perform activities of daily living (ADL’s) independently, improve self-confidence, and increase their quality of life. In comparison to past and present initiatives, the KitchenBot, aims to alleviate the need for valuable floor space, provide universal accessibility to all individuals with disabilities (i.e. those not using wheeled mobility), provide a simple control method for task execution, and present opportunities for needed capabilities, such as heavy payload tasks, that other designs are unable to meet.
AIMS
The purpose of this study is to obtain perceptions, opinions, and attitudes regarding the prototype design of the KitchenBot via focus groups. Furthermore, it is to confirm the proposed prototype track can meet safety design criteria via Finite Element Analysis (FEA).
METHODS
The proposed KitchenBot idea started with a mission to design an overhead mounting system for a dynamic robotic manipulator to assist individuals with physical disabilities for tasks associated within a kitchen environment. A panel of industry experts, including engineers, clinicians, and users populated a list of design criteria derived from user needs for the proposed KitchenBot idea. Namely, for example, the track and arm is discrete when unused, has a fail-safe braking system, is safe to be within close proximity of, can accommodate a payload of 50 [lbf], has the freedom to reach the entire kitchen workspace, can accommodate two arms at once, and can be easily installed into a private home setting. Numerous conceptual designs, aimed at satisfying each criterion, were sketched or modeled including a single and double column mounted articulating gantry crane, a three-point overhead cable suspension (like those seen in football stadiums for camera suspension over the field of play), an X-Y overhead motion carriage, a wall mounted track with a vertical telescoping carriage, and a wall mounted track with a vertical linear column. Ultimately, a decision matrix of the proposed concepts was evaluated and the latter was selected before further work began on the detailed design of the currently known KitchenBot.
The KitchenBot has three main components: First, an S-shaped wall mounted track for the motorized carriage assembly to ride. Second, a locking linear column that is driven horizontally, with an attached motorized vertical carriage to fasten a manipulator. Third, the commercially available six-degree of freedom robotic manipulator that mounts to the vertically moving carriage. Overall, it is this locking vertical and horizontal carriage that provides a relocatable and stable column for a dexterous or strong arm to provide assistance.
To evaluate the KitchenBot at its current state, a user-focused design review and technical review was conducted. Focus groups with wheelchair users were conducted to evaluate the current prototype design capabilities and provide further information related to the common difficulties individuals have in the kitchen. Furthermore, an FEA of the design was required to ensure the prototype would meet or exceed the expected physical loading caused by the most demanding but necessary kitchen tasks.
Focus Group Procedure
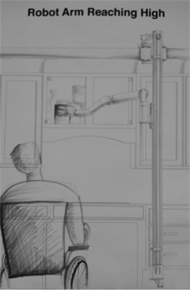
Subjects were recruited if they were over the age of 18, have a physical disability, and can comprehend English. All subjects were asked to provide informed consent before participation in the focus groups.
Participants first completed a questionnaire about general demographics and their current and past experience with assistive technology. They then participated in a round-robin group discussion moderated by one of the investigators. Each focus group consisted no more than 15 participants and lasted no more than 2.5 hours. During the focus group, subjects were presented with enlarged photos of the conceptual KitchenBot design (Figures 1 and 2). The discussions were audio recorded and later transcribed for content analysis. After the focus group discussion, subjects were also asked to complete a questionnaire on kitchen area difficulties, amount of use, and potential features in a new product such as the KitchenBot.
Finite Element Analysis Procedure
The focus of the FEA was on the curved track and the wall studs being used for mounting. The track was designed as a robust curved anodized aluminum assembly, supported by steel brackets that would be installed above existing kitchen cabinets. This S-shaped track provides the arm access to the entire kitchen, regardless of shape. Revision was made to reduce weight and complexity of the curved track. However, understanding structural stability of the curved track is imperative to ensure safety and the design would meet or exceed the requested design criteria of a 50 [lbf] payload.
The FEA analysis was performed using SolidWorks Simulation Tool. The input simulation parameters required defining each individual part’s material properties (i.e. yield strength, density, elastic modulus, etc.), defining the fixed-in-space faces of the wall studs, defining all bolt connections (including their torque, mass, and surface contact area), defining all non-penetrating surface contact pairs, and the applied loading (including gravity, torque, and payload). The output of the simulation provided a visual representation of stress, strain, deformation, and the factor of safety (FOS).
Focus Group Data Analysis
Descriptive statistics were used to summarize the data from the questionnaires. An investigator transcribed the focus group discussions and extracted discussion themes.
RESULTS
Subjects
A total of 25 subjects were recruited at the 2012 National Veterans Wheelchair Games (NVWG) to participate in 3 focus groups. Of those 25, 24 reported their disability as a Spinal Cord Injury (15), Multiple Sclerosis (4), Hemiplegia (1), Paralysis (1), Stenosis (1), Arthrogryposis (1), and having a bone disease (1). This population was of interest because of their experience with modified kitchen ADL’s. Of those 25 individuals, 12 use manual wheelchairs, 12 use power wheelchairs, and one uses a scooter for their independent mobility. There were 18 reported males and 5 reported females with, regrettably, an unrecorded average age.
Results from the focus group revealed almost one third (32%) of individuals ranked using the oven, using the stove-top, and putting away groceries as a 4 or higher on a 7 point scale of difficulty. Furthermore, as shown in Table 1, the top three features of the conceptual KitchenBot were handling hot objects, heavy objects, and reaching for items in the upper cabinets. One subject said during the discussion, “Even with a reacher, when you try to get something that is high or too heavy, it just falls.”
Item |
Mean |
SD |
---|---|---|
Opening cabinet doors, drawers, and appliances: |
5.3 |
2.1 |
Reaching items from the upper cabinets: |
6.1 |
1.5 |
Reaching items from the lower cabinets: |
5.0 |
1.9 |
Reaching items from the floor: |
4.7 |
2.0 |
Stabilizing items: |
5.3 |
1.8 |
Unloading the groceries: |
5.7 |
2.0 |
Unloading the dishwasher: |
4.5 |
2.0 |
Handling hot objects: |
6.1 |
1.5 |
Handling heavy objects: |
5.9 |
2.0 |
Control via "touch to move" interaction: |
4.3 |
2.2 |
Control with a joystick: |
5.0 |
2.3 |
Control with a tablet PC: |
5.6 |
1.9 |
Easily Hidden: |
5.1 |
1.9 |
Note: Scale ranges from 1 being less wanted to 7 being most wanted feature |
Based on focus group feedback, one of the most desired features of the KitchenBot is the ability to handle heavy objects, which reinforces the necessity of having a detailed structural analysis of the wall-mounted assembly. To test this, an applied load on the track’s most unsupported point was 50 [lbf] and a torque of 100 [ft-lbf]. What resulted was a stress level induced in the track between 27 [Mpa] and 200 [kpa], the brackets between 12 [Mpa] and 2.5 [Mpa], and the studs between 207 [Mpa] and 76 [Mpa]. All static stress values, as well as the negligible strain level, are well below the respective material’s yield point and indicative of a safe track. The maximum deflection of the track was a mere 0.059 [in]. This is an acceptable deformation because it does not exceed the elastic region of the material’s properties. Overall, as shown in Figure 3, the lowest Factor of Safety in the studs, which is a term used for describing the structural capacity of a system beyond the load, was found to be 2.5. These results show the track and building studs are safe when operating within the design criteria limits that can be regulated by the robot.
DISCUSSION
In a survey, one found similar results whereby both clinicians and potential users view lifting heavy objects as one of the tasks most important for a robotic manipulator to perform (Stanger et al., 1994). Furthermore, in another clinical evaluation among 24 high-level quadriplegics, the DeVAR system, as previously explained, demonstrated usefulness for performing daily activities and over 60% of individuals preferred the robot rather than an attendant for preparing meals, self-feeding, and brushing teeth (Hammel et al., 1989). Further design, refinement, and analysis of the KitchenBot could yield similar results with further benefits.
For a number of reasons, the proposed overhead track mounted robotic manipulator for the kitchen aims to provide a system more practical for the mass market. First, a broad range of individuals could utilize the KitchenBot who have upper extremity impairments, including those who do not use powered or modified mobility. Second, the KitchenBot aims to be part of a kitchen to eliminate issues with maneuvering, as compared to manipulators on a wheelchair or mobile base. Third, the systems fixed installation provides good mechanical stability, adaptation for the environment, and control simplicity (Balaguer et al., 2006). To explain further, good mechanical stability implies potential for high payload tasks, which cannot be achieved by existing mobile base and wheelchair-mounted manipulators. Adaption for the environment implies the KitchenBot could be installed in varying configurations of workspace and control simplicity suggests the software development is far less complicated than its counterparts because it will stay in a confined workspace.
The KitchenBot has potential to become a residential appliance for those who require the next level of assistance beyond a caregiver. The initial prototype design presented above, although unique to HERL’s building space, is transferable for use in residential homes with standard building materials. Additionally, the low-profile track requires little space above cabinets for installation that is consistent among typical residential kitchens. The next steps of the KitchenBot design process will be to hold reoccurring meeting of potential lead users, continue manufacturing and analysis, and conduct a usability study among the targeted population of elderly and disabled.REFERENCES
Balaguer, C., Gimenez, a., Huete, a. J., Sabatini, a. M., Topping, M., & Bolmsjo, G. (2006). The MATS robot: service climbing robot for personal assistance. IEEE Robotics & Automation Magazine, 13(1), 51–58. doi:10.1109/MRA.2006.1598053
Broeks, J., Lankhorst, G., Rumping, K., & Prevo, A. (1999). The long-term outcome of arm function after stroke: results of a follow-up study. Disability Rehabilitaiton, 21(8), 357–364.
Feinberg, L. F., Wolkwitz, K., & Goldstein, C. (2006). Ahead of the Curve: Emerging Trends and Practices in Family Caregiver Support. National Center on Caregiving.
Hammel, J., Hall, K., Lees, D., Leifer, L., Van der Loos, M., Perkash, I., & Crigler, R. (1989). Clinical evaluation of a desktop robotic assistant. Journal of rehabilitation research and development, 26(3), 1–16. Retrieved from http://www.ncbi.nlm.nih.gov/pubmed/2754623
Holliday, P., Mihailidis, A., Rolfson, R., & Fernie, G. (2005). Understanding and measuring powered wheelchair mobility and maneuverability. Disability and Rehabilition, 27(16), 939–949.
Schoenborn, C. a, & Heyman, K. M. (2009). Health characteristics of adults aged 55 years and over: United States, 2004-2007. National health statistics reports, (16), 1–31. Retrieved from http://www.ncbi.nlm.nih.gov/pubmed/19697804
Srinivasa, S. S., Ferguson, D., Helfrich, C. J., Berenson, D., Collet, A., Diankov, R., Gallagher, G., et al. (2009). HERB: a home exploring robotic butler. Autonomous Robots, 28(1), 5–20. doi:10.1007/s10514-009-9160-9
Stanger, C. a., Anglin, C., Harwin, W. S., & Romilly, D. P. (1994). Devices for assisting manipulation: a summary of user task priorities. IEEE Transactions on Rehabilitation Engineering, 2(4), 256–265. doi:10.1109/86.340872
Taylor, B., Cupo, M. E., & Sheredos, S. (1993). Workstation Robotics : A Pilot Study of a Desktop Vocational Assistant Robot. AMJ Occup Ther, 47(11), 1009–1013.
Xu, J., Grindle, G. G., Salatin, B., Vazquez, J. J., Wang, H., Ding, D., & Cooper, R. A. (2010). Enhanced Bimanual Manipulation Assistance with the Personal Mobility and Manipulation Appliance (PerMMA). IEEE/RSJ International Confrence on Intelligent Robots and Systems, 5042–5047.
ACKNOWLEDGEMENT
The VA Center grant #B6789C and the Rehabilitation Services Administration grant #H129E100001 from the Dept. of Education supported this research. This material is the result of work supported with resources and use of facilities at the Human Engineering Research Laboratories, VA Pittsburgh Healthcare System. This material does not represent the views of the Department of Veterans Affairs or the United States Government.